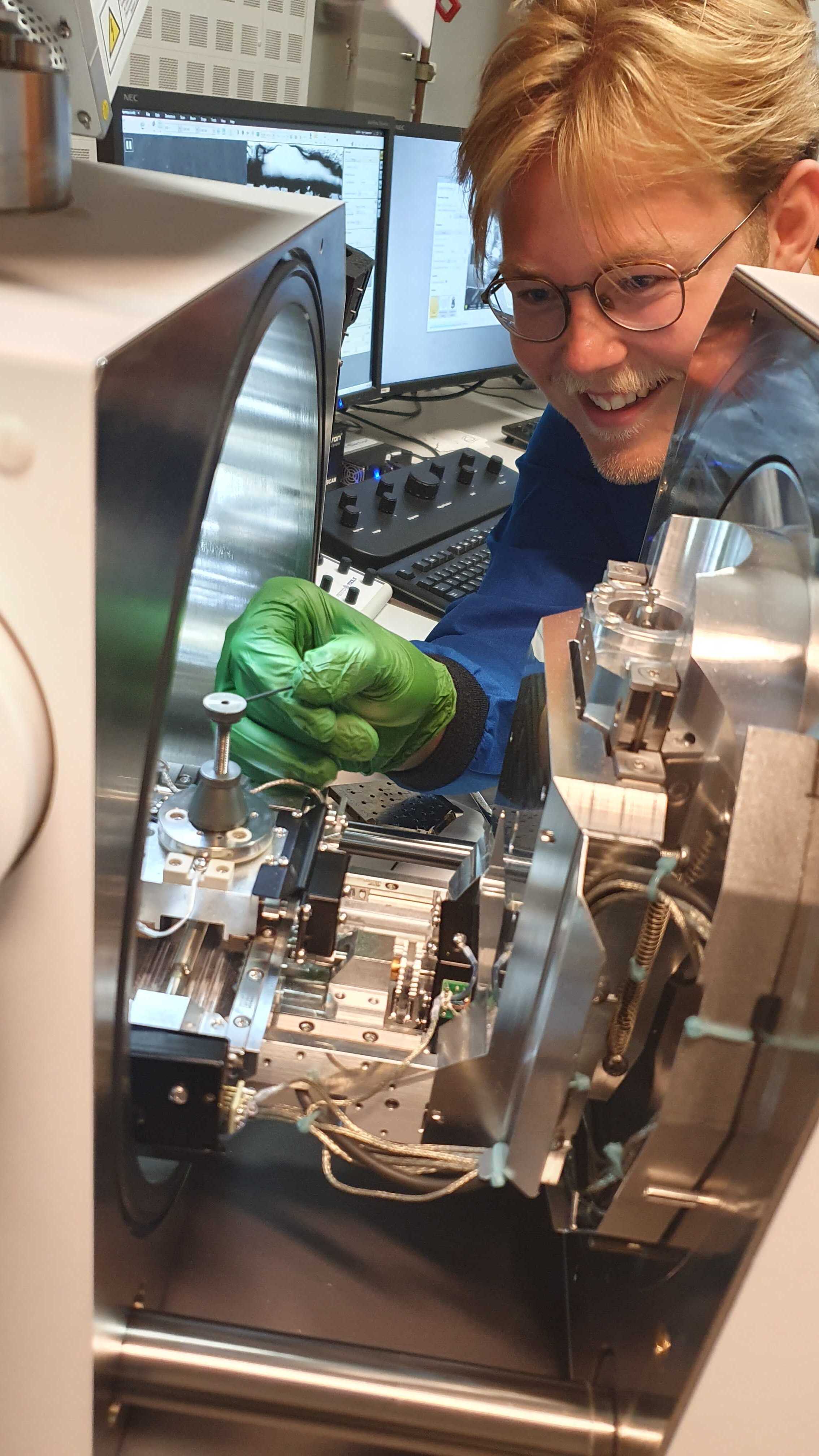
Additive metal manufacturing, commonly referred to as 3D-printing, is redefining the boundaries of material design. Such innovations have the potential to improve the fabrication of lightweight and heat-resistant components, which could contribute to reductions in carbon emissions. Among recent advancements, the 3D-printing of stainless steel via Laser-Powder-Bed-Fusion has been shown to facilitate local tailoring of microstructures, enabling distinct mechanical properties within different regions of a single 3D-printed component. In this study we delve into the attributes of 3D-printed 316L stainless steel focusing on microstructural features, such as the dislocation cells emerging from the rapid cooling post-printing and crystal orientations. A 316L stainless steel sample, created with Laser-Powder-Bed-Fusion and chemically etched, underwent 300 nanoindentation tests that utilize a microscale diamond tip to measure hardness and strain rate sensitivity. Scanning Electron Microscopy provided insights into the dislocation cells' sizes and shapes around each indent, while Electron Backscattering Diffraction revealed the local crystal orientations. The results from this substantial dataset reveals a disparity in the mechanical properties between those surfaces aligned parallel and those perpendicular to the 3D-printer's build direction. A series of inverse pole figures further illustrates how hardness and the size and shapes of dislocation cells vary based on local crystal orientations. Surprisingly, one finding challenges current theories regarding dislocation cell growth, suggesting the presence of a potentially novel dislocation cell texture