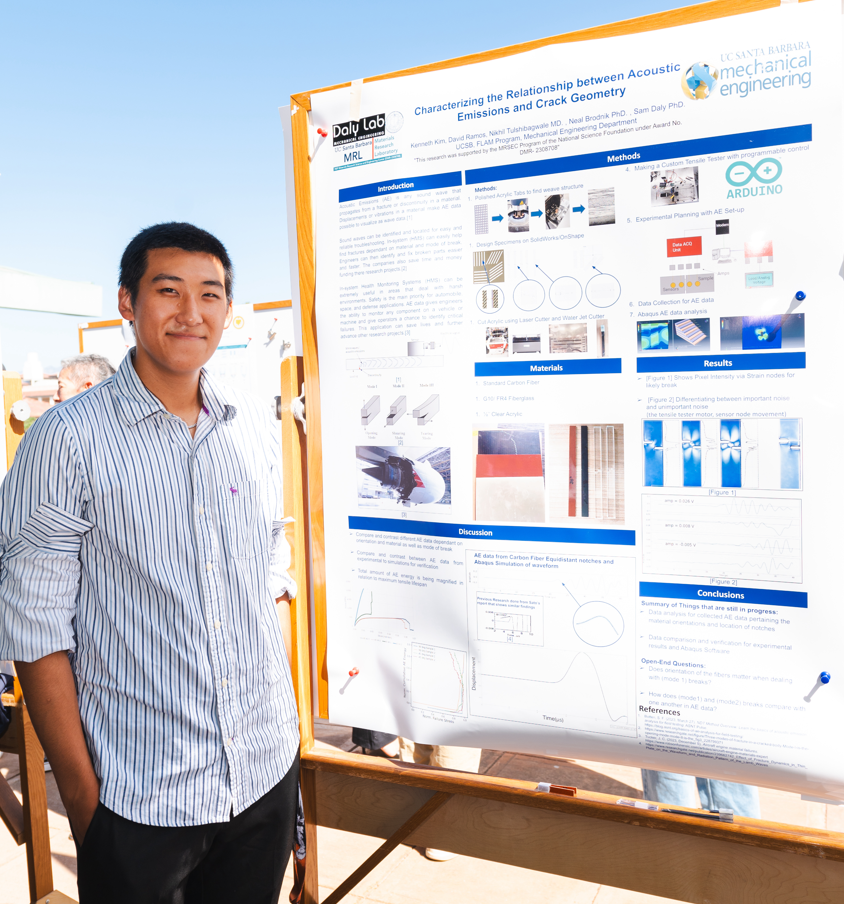
Acoustic Emissions (AE) are any sound wave that is propagated from a fracture in the material. The importance of characterizing these AE waves is its relationship between sound and crack propagation. Acoustic Emissions are particularly promising for structural health monitoring (SHM) of advanced composites subject to extreme environments in space and defense applications. Cracks can occur at any point of tension or compression and finding the source of cracks in complicated machinery is inefficient and costly. In-system SHM will give engineers the ability to identify problems easier and maximize the lifetime of costly, complex components with broken parts. Further experimental work is currently needed to develop quantitative relationships between AE signal and crack geometry, i.e., crack orientation, size. The present work is focused on two experimental thrusts: (i) tensile testing of carbon fiber and fiberglass epoxy laminates, cut at 0, 30, 60, 90 to promote damage in different orientations and (ii) fracture testing on laser-cut acrylic samples. These tests will be equipped with a custom-built tensile tester. Microphones will be attached to the specimen to output AE signals that can be digitally read on a computer. The experimental data will be analyzed in tandem with simulation results in simplified, representative scenarios to assess the relationship between sound waves and the materials maximum tensile strength and modulus of elasticity.