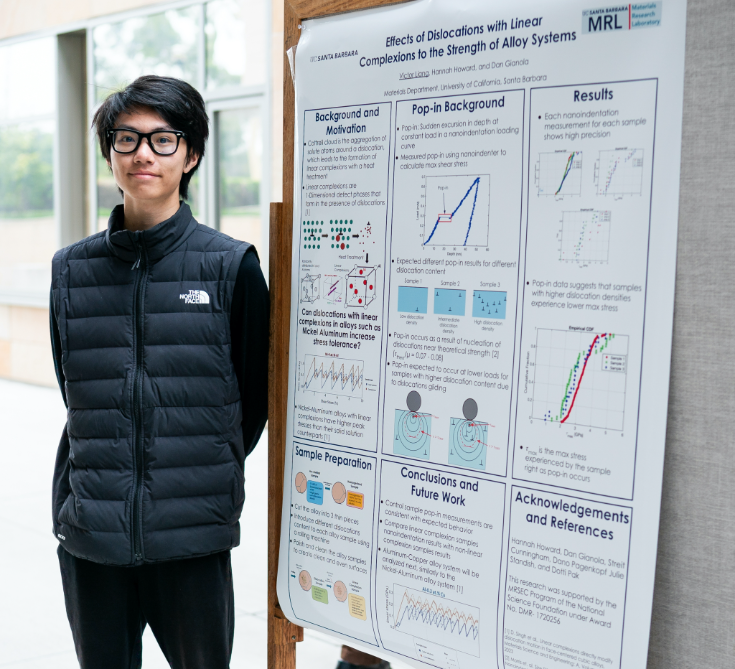
Both dislocations and secondary phases in alloys are known to increase stress tolerance, but it is not always known how dislocations impact phase evolution. Linear complexions are one- dimensional defect phases that form in the presence of dislocations due to solute segregation and annealing to induce defect phase transformation. This project aims to understand how linear complexions form around dislocations in a nickel-aluminum alloy, show that dislocations with linear complexions increase stress tolerance, and to what extent those dislocations with linear complexions impact stress tolerance. Samples were made via a cold-rolling process to different plastic strain values in order to introduce different dislocation populations in each sample. To evaluate how the dislocations impact material properties, nanoindentation was used to measure incipient plasticity events known as “pop-in.” A pop-in is a sudden excursion in depth at constant load in a nanoindentation loading curve and can occur as a result of nucleation of dislocations near theoretical strength. They are expected to occur at lower loads for samples with higher dislocation content due to dislocations gliding. Future work will include exploring how linear complexions form around dislocations in aluminum-copper alloys and nanoindentation of samples after a second heat treatment to induce linear complexions. Understanding how dislocation density impacts localized phase transformation around these dislocations can help inform future alloy design for improved material properties.