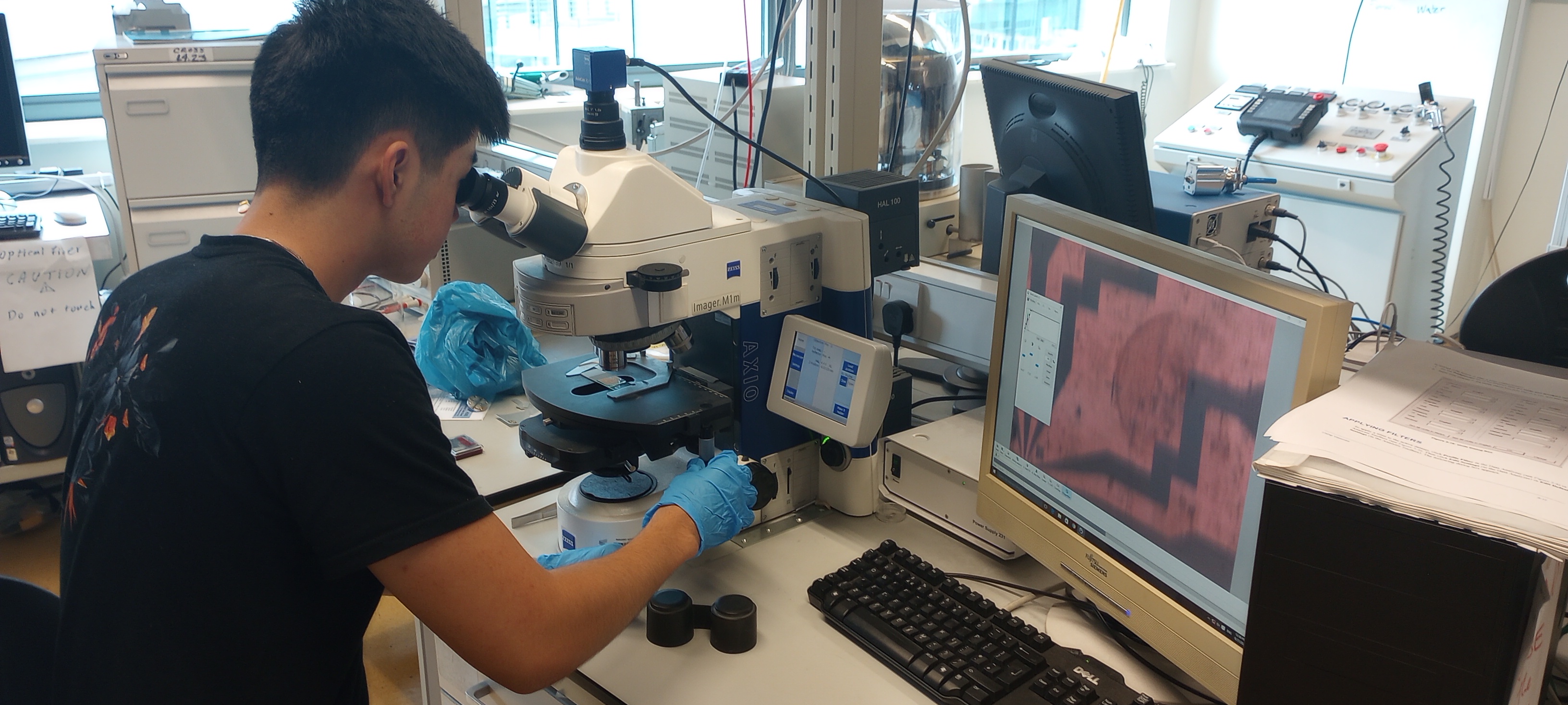
The focus of this project is to develop new methods for characterizing materials via small scale indentation. This process is commonly done on a nano indenter which uses a tip of specified geometry to indent a sample. Knowledge of the tip shape function is combined with measured force and penetration data to calculate modulus and hardness. This project does this with an AFM (Atomic Force Microscope) with the berkovich tip shape, which is the gold standard shape used for small-scale material mechanical characterization. An AFM manipulates a very sharp tip located at the end of a microfabricated cantilever to form profilometric-like images of a surface. Cantilever deflection and vertical sample displacement are simultaneously measured by the AFM. By calibrating the cantilever and performing some calculations, force and penetration data can be extracted, similar to that obtained with a nanoindenter, allowing modulus and hardness to be calculated usually by the Oliver-Pharr analysis method. There are many benefits to indenting with an AFM such as cost of equipment, ease of imaging, and possibility of indenting at faster speeds and on different materials. After correcting for things such as tilt of the cantilever, Berkovich shaped indents were achieved. The results for low indent depth were fairly repeatable while deeper depths were not. The resulting data provides a first estimate of modulus and hardness which are not very accurate. The results could be influenced by a range of small scale attractive and repulsive forces between the tip and sample as well as the effects of the bending cantilever during indentation. However, the consistency in results are promising towards the ability to apply corrective procedures to extract meaningful characterizations. Ultimately, for indentation with AFM more analysis is required but it is hopeful that this process can eventually be used to provide insight into material characterization.